Sample Inspection Report for a House
Dear Mr. and Mrs. Home Buyer,
The pages to follow contain your TOTAL HOME INSPECTION report, which is based on observations made while conducting an inspection of ANY HOUSE, FAIRFIELD COUNTY.
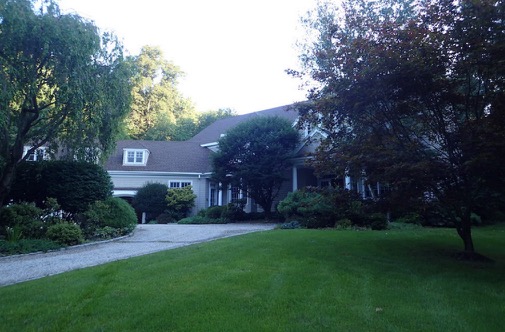
The purpose of this inspection was to assess and report the condition of the dwelling through a primarily visual inspection and when possible an operational check of its unconcealed, observable and accessible major components. Our inspection and this report do not identify, nor are they intended to identify, every minute or latent defect. The inspection and report do identify, in general accordance with the State of Connecticut's Home Inspection Standards of Practice, the systems and components that are near the end of their serviceable lives and the significant defects or deficiencies of the systems and components our inspector identified at the time of your inspection.
Your inspection and this report will provide you with enhanced general insight and useful information about the house, and will contain comments that should help you better maintain it should you become its owner. As one example, because water and moisture are the root cause of many problems in dwellings of all kinds, any and all references to water or moisture, no matter how small, should be taken seriously and acted upon.
You were issued a copy of relevant sections of the State of Connecticut Regulation Concerning Home Inspectors (the "Standards of Practice & Code of Ethics"). We recommend that you retain this copy of the Standards of Practice & Code of Ethics in the event that you need to better understand the scope and purpose of your home inspection.
As you read our report, know that we frequently reference specific locations inside or outside the house. For clarity's sake, please keep in mind that locations are frequently expressed as if from a vantage point at the front of the house, as if we are facing it. If we write, "the rear left bedroom", rear means the section of the house farthest from the vantage point, and left means the part of the house to the left of the vantage point.
Performing a TOTAL HOME INSPECTION for you and providing this report has been our privilege. Should you have any questions concerning this report or if we can be of further assistance in any way, please do not hesitate to contact our office.
Landscaping
The trees were in generally acceptable condition. With proper maintenance and an open tree canopy the trees should flourish.
There are branches touching and overhanging the roof and gutter system (see photos left and right for example areas). By trimming or removing them, you will likely reduce roofing, gutter and siding maintenance and repair and you will also remove a potential bridge for animals.
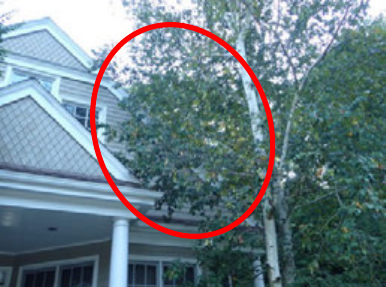
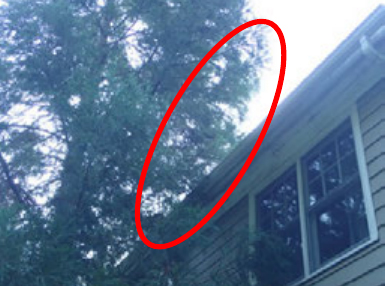
There are trees, which appear to be dead, at the rear left of the property (see photos left and right). We recommend that the trees be removed for your safety and to help prevent harm or damage should the trees fall.
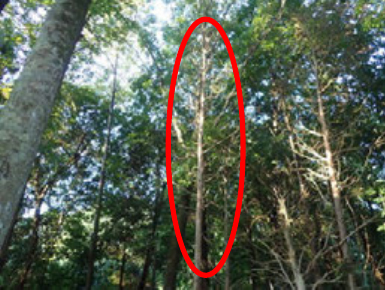
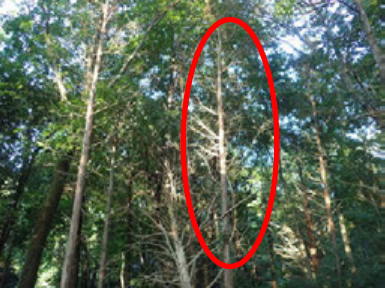
There are also fallen trees at the rear of the property (see photos left and right for examples). We recommend that the trees be removed for your safety and to help prevent an environment conducive to attract insects.
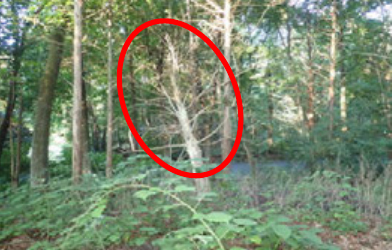
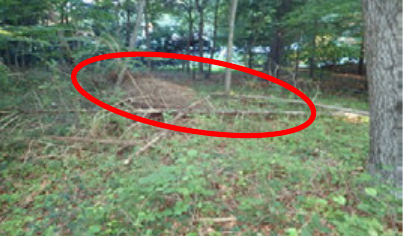
The shrubbery needs pruning (see photo right for example area). Trimming the plantings away from the foundation and building to afford a minimum of twelve inches of clearance between the shrubs and exterior cladding will help prevent moisture from being trapped against the structure, potentially promoting rot on and beneath vulnerable exterior components.
The tendrils of the vines clinging to the rear left center chimney and to the siding as well as the foundation (see photos left and right for examples) can damage the chimney structure and to the siding as well as the foundation and to the vulnerable exterior cladding and the materials beneath the siding and trim components in these areas. The foliage can also provide an inviting environment for moisture and insects. Consider removing the offending vines.
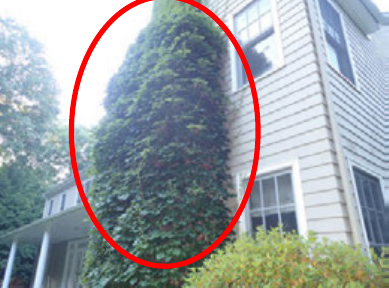
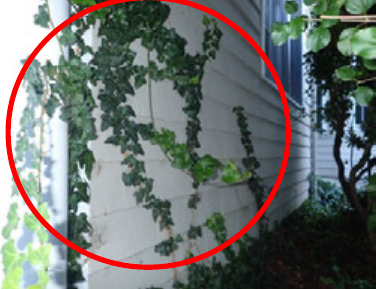
The lawn was in generally acceptable condition, although spotty areas were observed. With an open tree canopy and proper, consistent maintenance, the lawn's appearance would likely improve over the next year or two.
Evaluating irrigation systems is beyond the scope of the standard home inspection we performed for you. As a result, we offer no evaluation of the installed irrigation system in this report. We recommend that you contact the installing contractor or the company that opens and closes the system to inspect the system and render a written evaluation of its condition. At that time the installing contractor or the company that opens and closes the system should instruct you as to the system's proper operation.
Most of the perimeter grading around the foundation was only marginally pitched, which could result in water collecting against the foundation. At least six feet of pitch should be maintained, with a minimum of 1 inch per foot, for all soil grading away from the foundation. This will aid in proper drainage of roof and surface water, which will help minimize pressure on the foundation walls and help minimize the chance of water seepage into the lower level of the building.
If water infiltration into the lower level becomes a problem, it may be necessary to install a curtain drain in the rear yard to divert the flow of ground and surface water away from the foundation.
It may be necessary to install a window well around the front right side basement window (see photo below left) in order to build up the soil level as recommended above. Keeping the new well clean and keeping clean the existing windows wells at the left side of the house and the rear right side of the house (see photos below right and below left and right – 2nd row) will help avoid an inviting environment for insects or rot and help permit the at-grade or sub-grade levels to be properly ventilated when necessary. We recommend that the wells be protected with a clear plastic cover to prevent water accumulations in the wells, and to help minimize pressure on the foundation walls and possible seepage into the at-grade or sub-grade levels.
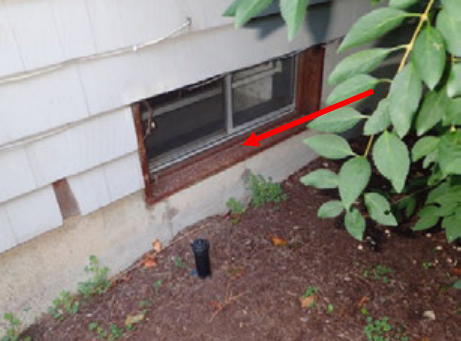
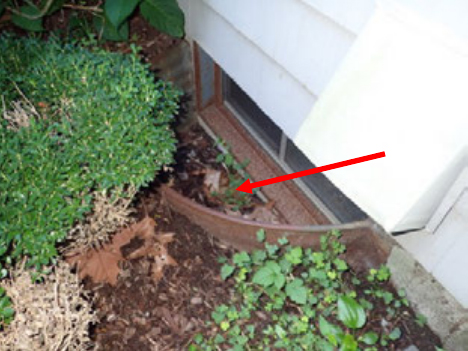
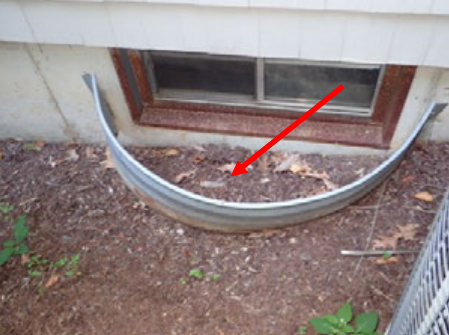
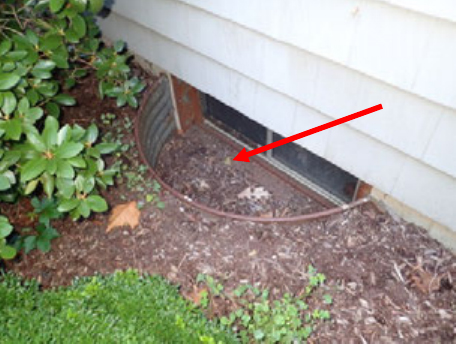
Inspecting swimming pools is beyond the scope of a standard home inspection. As a result, no evaluation of the swimming pool (see photo left), its equipment (see photo right for example of pool equipment) and surrounding structure will be included in this report. We suggest you have the service company or persons responsible for the pool maintenance render an opinion as to its condition. It should be noted that the Consumer Protection Safety Commission recently re-issued its pool barrier guidelines and its drain cover regulations in 2009. Some of these regulations can be found on the internet (www.cpsc.gov). Full compliance with these guidelines or any more recent guidelines will help protect your children and the neighborhood children. We also recommend that you periodically clean the pool and its components with appropriate anti-bacterial agents for health purposes. The firewood on the rear entrance landing/patio (see photo right) should be relocated. Firewood should never be stored inside nor in such close proximity to a building structure, as it is an environment conducive to attracting insects. Moving the firewood to a location as far away from the structure as is practical is recommended.
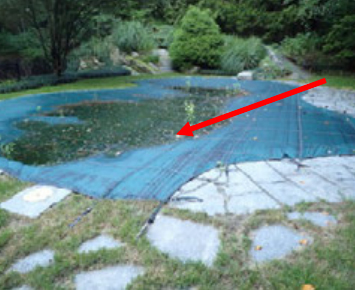
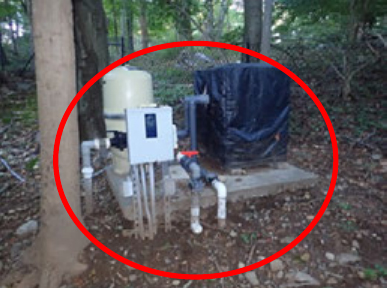
The firewood on the rear entrance landing/patio (see photo right) should be relocated. Firewood should never be stored inside nor in such close proximity to a building structure, as it is an environment conducive to attracting insects. Moving the firewood to a location as far away from the structure as is practical is recommended.
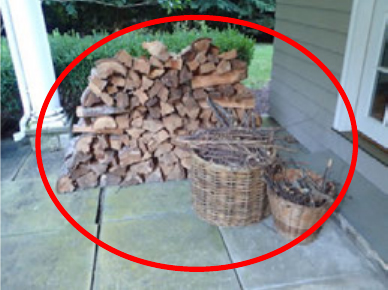
Driveway & Entrance
The driveway approach, drainage, surface, lighting, turnaround area and walks were in acceptable condition.
It is important that your house number be displayed on the surface of the house. Consider installing the number so that it may be seen from the driveway by day or night, which would be beneficial in the event of an emergency.
Keeping the wooden, rear left center entrance landing surfaces and its structural components treated with a quality wood preservative, paint or stain will help prolong the landing's life (see photo right – red arrow). Secure the loosely installed slate stone “step” at the rear left center entrance (see photo right – white arrow) for your safety and for your convenience.
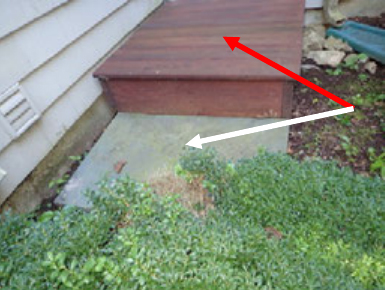
Keeping the entrances clear of leaves, debris and snow accumulations will help prevent water intrusion into the lower levels and living areas, and will help reduce the likelihood of rot developing at vulnerable wood components.
We recommend that you confirm the condition and functionality of all exterior lighting, prior to your closing, for your safety and for your convenience.
Building Exterior
The roofs are gable, shed and hip styles. The roofs are clad with asphalt shingles in an architectural design pattern. The roof was inspected from its surfaces.
The roof surfaces were in acceptable condition.
Portions of the roof flashings were inaccessible for inspection. The visible roof flashings appeared to be in acceptable condition.
There were exposed nail heads observed on the lower front center roof flashing (see photo right) that should be sealed as required to help ensure that no precipitation can infiltrate the roof cladding and substrate.
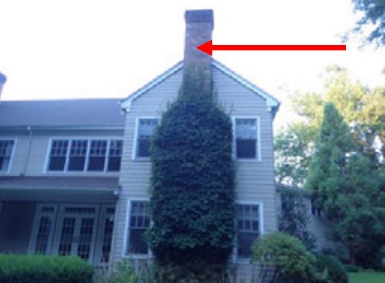
The chimneys are masonry (see photos below left for views of the chimneys from the ground and photos below right for views of the same chimneys from the roof surfaces). The chimneys were in generally acceptable condition.
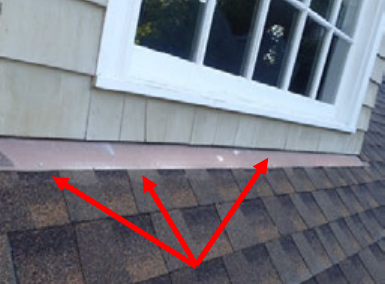
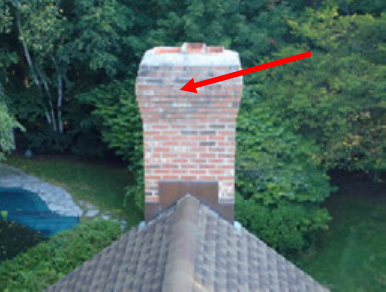
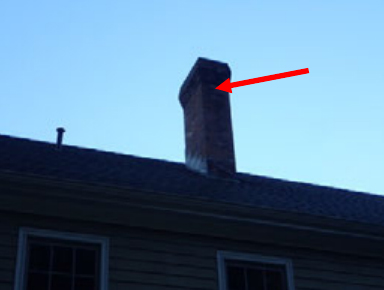
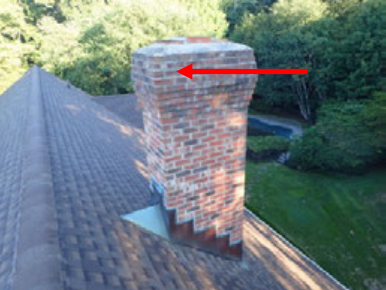
Our inspector was unable to safely access the tops of the two masonry chimneys therefore the interiors of the chimneys' flues could not be inspected from those vantage points.
We recommend that all chimney flues be covered with a screened cap to prevent animals from nesting in the chimney and to prevent water from affecting the structure.
The cracks in the rear right chimney’s crown (top of chimney – see photo right) should be sealed to prevent moisture from seeping behind the bricks and causing damage to the structure.
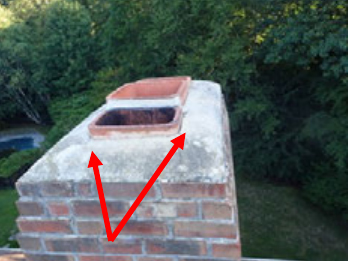
The gutters were in generally acceptable condition, but there is a sagging section of the guttering system at the front left corner of the house (see photo below left), a section of loosely installed gutter at the rear left of the house (see photo below right) and a disconnected leader at the front right side of the house (see photo below center (2nd row). These sections of the guttering system's continued use in their present condition will likely cause damage to the fascia boards, soffits and surrounding wood members in that area. Due to the fact that it was not raining at the time of this inspection, it should be noted that it is virtually impossible for anyone to detect gutter leaks, except as they are occurring or by specific water tests, which are beyond the scope of the standard home inspection we have performed for you. Periodically check all joints for leaks and caulk where it is required. All gutters should be pitched toward their downspouts and the leaders should terminate as far from the building as practical. Gutters and rain leaders must remain free flowing at all times.
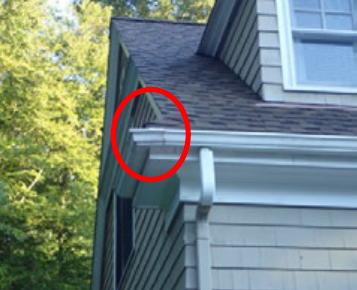
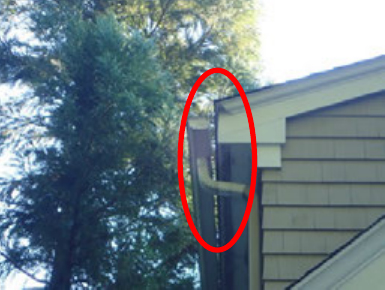
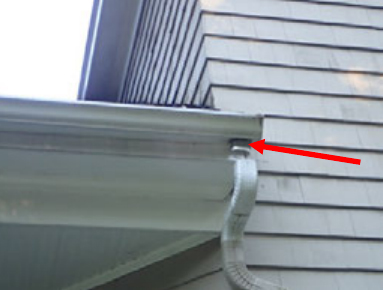
All rain leaders terminating into in-ground receptacles must remain free flowing at all times (see photo right for example of an in-ground receptacle). Underground systems are vulnerable to clogging and should be checked annually. The rain leaders that do not terminate into an in-ground receptacle (see photo above left for example) need to be extended as far away from the foundation as practical to prevent roof water from collecting against the house and seeping into the lower level.
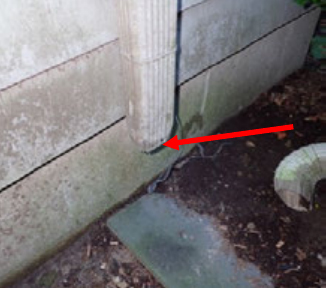
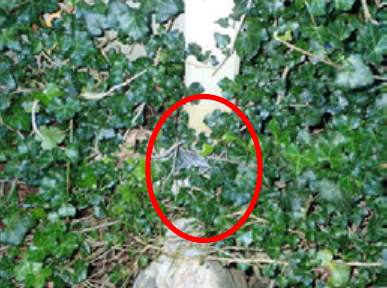
Portions of the guttering system require cleaning now and at least every spring and multiple times during the fall in the future (see photo right for example of offending area). If these gutters are not cleaned, you will experience ant infestation and a general rotting condition.
The primary windows are wood-framed, double-glazed (insulated), double hung sashes. They were in generally acceptable condition. The windows' tracks should be kept clean and lubricated for ease of operation.
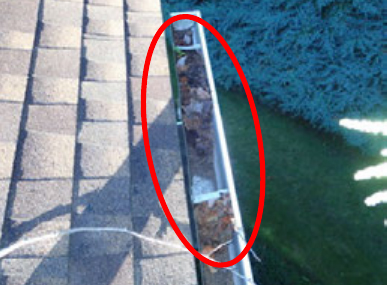
It is common, after a period of time, for insulated glass panels to lose their vacuum seals and develop condensation and/or fogging between the layers of glass. This is normal and eventually happens to many insulated glass windows. While we make every effort to identify the loss of insulated window seals, the identifying characteristics can vary in magnitude from totally fogged windows to barely visible fogging or condensation. Weather conditions, sunlight (direct sunlight or the lack of sunlight), curtains, shutters and other obstructions contribute to making identification of these seal failures difficult at times and sometimes impossible. For these reasons TOTAL HOME INSPECTION cannot ensure that the insulated seals have not failed on the insulated windows in this house. All references to or omissions of references to failed insulated window seals in this dwelling should not be construed as an exhaustive or authoritative evaluation by TOTAL HOME INSPECTION.
There was loosely installed and torn screen at the family room’s rear left window. The screen should be secured and repaired or replaced as required for your comfort and convenience. Remember that window screens are not designed to prevent children from falling out of the windows. We recommend that you prevent children from getting too close to any windows.
The house is clad with wooden shingle siding as well as with wood trim. They were in generally acceptable condition. Sealing all penetrations, seams, and voids in the siding, as well as at the window and door casing perimeters, the unions between siding and trim components and the unions between exterior cladding and foundation will help to establish and maintain a weather tight envelope for the house, and will protect the siding and substrates from exposure to moisture and deterioration.
There are areas around the house where the siding was too close to, or even in contact with the soil. This will eventually lead to a rotting condition and will invite insect activity. Cut the grade or remove lower courses of siding in these areas, so that at least 6" of foundation is exposed. This would lend itself to a healthier wood environment. Keep these areas free from debris so that it can be inspected for any rotting or insect evidence.
There are areas of garage door trim that were embedded in the driveway surface (see photos left and right for examples). This will eventually lead to a rotting condition and may invite insects. Keep these areas free from debris and inspect them for rot or insect infestation annually.

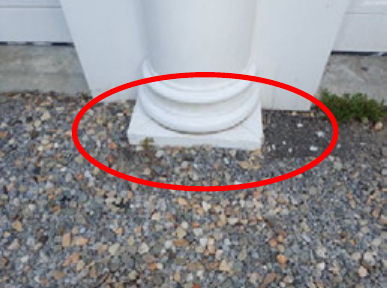
There were places around the house where rot or the onset of wood rot was observed, for example front left corner garage door trim/pillar base, at the family room rear left side window trim, at the rear right family room window trim, at the rear right landing/patio pillar base, at the rear left center family room window trim and at the front entrance pillar base (see six photos below for examples). This and all rotted or potentially rotted wood should be removed, and the sub-surfaces should be repaired as necessary. When the sub-surfaces are repaired, new wood should be installed, caulked and painted. Potentially rotting wood that is not repaired remains an invitation to insect infestation. When the sub-surfaces are exposed, if any insect activity is found, it should be treated as necessary at that time.
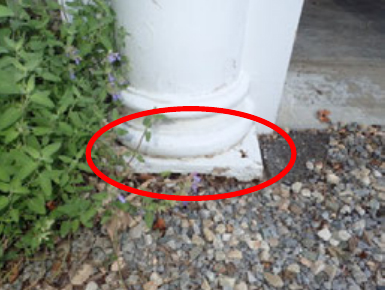
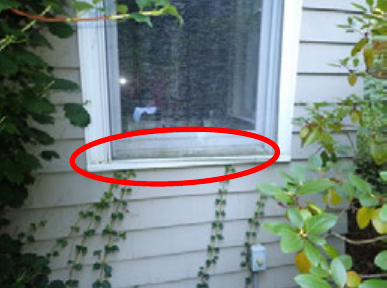
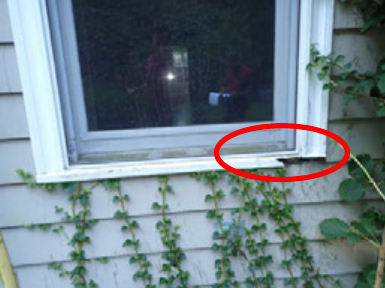
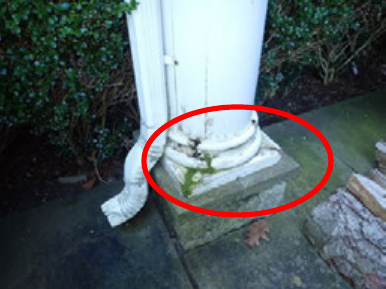
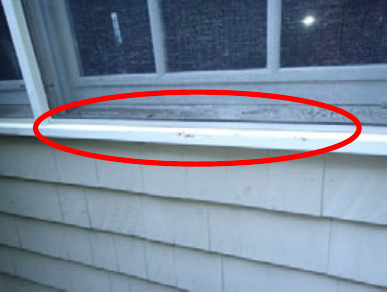
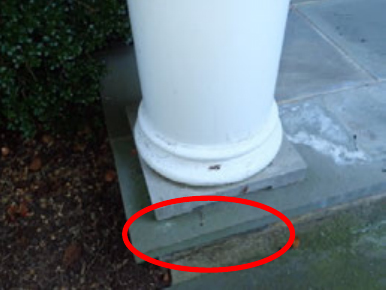
The exterior was peeling and stained in some areas, but it was generally in acceptable condition. Plans should include refinishing the offending areas in the future to help ensure a weather tight seal.
We observed gaps, voids and open mortar joints as well as a loose slate stone in the front right corner slate stone surface (see photo left) that should be repaired to help prevent water infiltration and damage to the patio and potentially to the patio substrate, at-grade and sub-grade foundation and interior spaces.
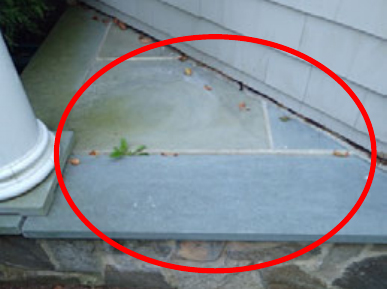
Water was supplied to the right side exterior hose bibcock (faucet) at the time of this inspection. No water was supplied to the rear left, rear yard (near the gazebo) and rear left exterior hose bib cocks (faucets - see photo right for example of exterior hose bibcock) at the time of this inspection. We recommend that the water supply to all exterior water sources and freeze vulnerable water sources are turned off in the autumn and that all hoses are disconnected from the faucets, to help prevent damage caused by pipes that may freeze. Inquire with the seller as to the locations of the inside shut off valves for these hose bibs.
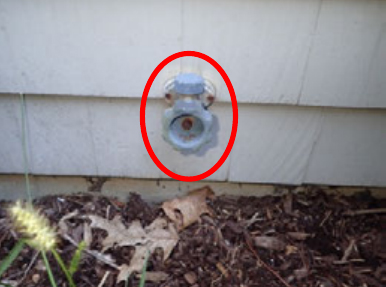
The State of Connecticut Regulation Concerning Home Inspectors (the "Standards of Practice & Code of Ethics") does not include inspecting or evaluating out-buildings and/or recreational structures, like the gazebo in the rear left yard, the swing in the front yard and the “tree house” in the rear yard area, therefore our home inspector did not inspect or evaluate the gazebo or its components or the swing in the front yard and the “tree house” in the rear yard area and their components.
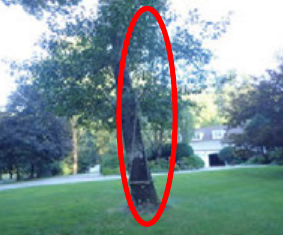
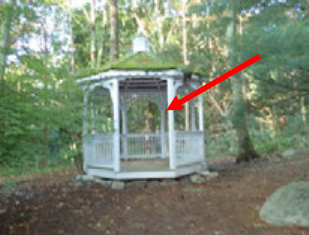

A propane gas (LPG) tank was buried at the rear left planting area of the house (see photo left). The shut off valve is located under the top cover of the buried tank (see photo right).
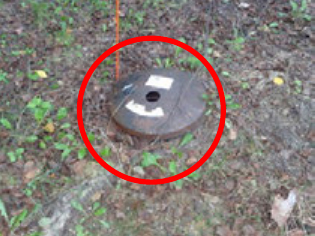
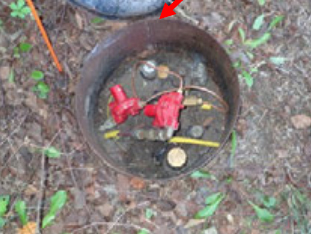
Sewage Disposal
It has been reported to our office that this house has been connected to a private septic system. This septic system was not inspected by TOTAL HOME INSPECTION. It was indicated that a septic contractor will evaluate this system soon after your home inspection. We do recommend that you acquire from that septic contractor some type of assessment of the system, which includes the tank, free flow of lines and general condition of the system. Properly sized septic systems should be cleaned and inspected every two years.
Basement & Structure
It was indicated to us that this house is approximately 23 years old, with apparent renovations, modifications and maintenance performed since its original construction. It is a two-and-one half story, colonial styled, wood-framed dwelling with a finished basement. Approximately 55 percent of the basement has been finished into a living space.
The basement was accessed by a stairway from the first floor and it was inspected from within.
The foundation walls are poured concrete and concrete blocks. Settlement cracks were noted in the foundation at the time of the inspection (see photos left and right for examples). Settlement cracks are not uncommon and are usually the result of improper soil grading around foundations. This condition is presently not a structural problem. It must be noted that settlement cracks could develop into structural cracks. Periodic inspection of these cracks and proper care should prevent future problems. These cracks should be filled from the exterior with a suitable material to help prevent seepage and they should be monitored for any further movement.
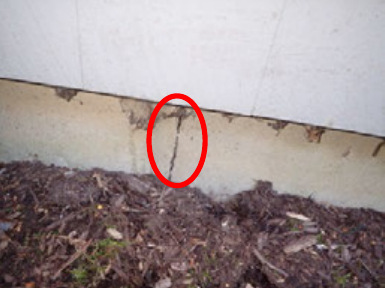
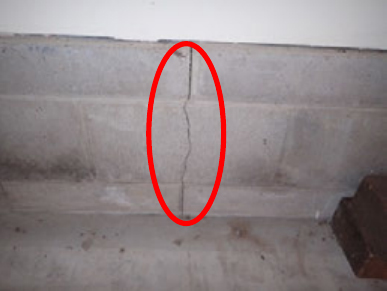
The visible cracks in the basement concrete floor appear to have been caused by normal expansion and contraction, and in our opinion, do not pose a problem at this time. The cracks should be filled and sealed to minimize the potential of moisture and radon infiltration into the basement.
The framing for the stairs from the garage to the basement is supported by a 4” x 4” wooden post. The post was cracked (“checking”), a bit bowed and it was twisted (see photo right). We recommend that this post be replaced by a properly installed concrete filled, steel cased, Lally column.
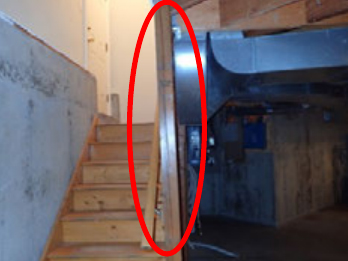
The main girders are built up, 8” and 10” manufactured, laminated wooden beams, while the first-floor joists are 2" x 10" 's installed 16" on center. The exterior walls appear to be 2" x 4" 's installed 16" on center. The girders are supported by concrete filled, steel cased, Lally columns and by the foundation walls.
Because of the finished ceiling, we were unable to visually inspect the majority of the first-floor structural components. Where visible the aforementioned structural components were in generally acceptable condition. Installing insulation beneath the first-floor sub flooring in the basement, like the insulation installed in the storage/utility room at the bottom of the stairs to the basement, will likely lead to improvements in energy efficiency and comfort. Consult an insulation reference or contractor for informative guidelines in this regard.
The visible insulation beneath the first-floor sub flooring in the storage/utility room at the bottom of the stairs to the basement was installed upside down. Conventional wisdom dictates that the vapor retarder should be installed closest to the living space above the sub flooring. Properly installed insulation will likely lead to improvements in energy efficiency and comfort as well as help restrict the flow of moisture from the warmer conditioned area to the cooler unconditioned area. Consult an insulation reference or contractor for informative guidelines in this regard.
An inspection and probing of visible and readily accessible areas was performed. No signs of active termites were noted at the time of this inspection. There are areas that do not lend themselves to inspection or probing such as the finished basement areas and the insulated box sills (top of foundation wall). It must be noted that we do not/cannot perform destructive testing/inspections. We cannot determine or confirm any insect activity or damage to areas that are not visible for inspection. The termites may not become visible until they swarm or build shelter tubes, so complete assurance of termite absence in these areas cannot be ascertained. Annual inspections are recommended.
As representative measures toward controlling general dampness in the lowest level areas, we recommend that the cold-water lines be insulated and that you consider installing at least one fan to enhance airflow and at least one dehumidifier to actively extract moisture from the areas.
Watermarks were evident in the basement area. This indicates water has entered this area in the past. The basement was dry at the time of the inspection. Be sure that all exterior grades pitch away from the foundation and extend the guttering system as far away from the foundation as practical (see LANDSCAPING and BUILDING EXTERIOR sections of this report). It must be noted that any area below grade is susceptible to water seepage during certain weather conditions. If after performing the above recommendations, water seepage is still evident, consultation with a waterproofing specialist may be necessary.
Black, microbial growth-type staining was observed in the basement on the PVC water supply pipes servicing the sprinkler system (see photos right and left for examples). This condition is usually the manifestation of a space that requires additional ventilation and/or dehumidification. Add ventilation and/or dehumidification as necessary to help prevent microbial growth.
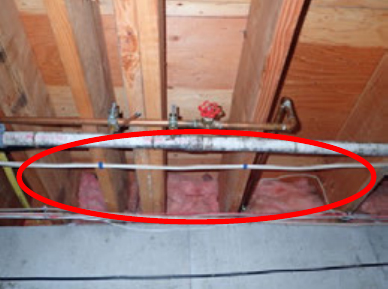
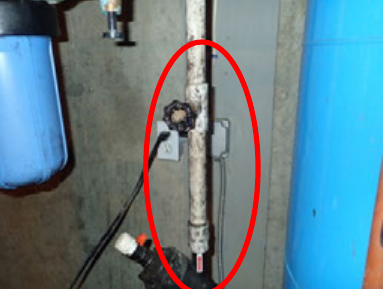
Determining the presence or absence of mold, pathogenic and/or toxic substances inside or outside the dwelling is beyond the scope of the standard home inspection we have conducted for you. The determination to have a mold test or evaluation performed or to correct an identified mold condition is entirely yours, and should be done based upon the full scope of information available to you through your own due diligence.
OmegaFlex brand, "Tracpipe" corrugated stainless steel tubing (CSST) was observed in the basement, apparently servicing the propane-fired kitchen cook top burners (see photos above left and right for examples). This type of flexible tubing has thin walls and would be vulnerable to splitting in the event of the house incurring a lightning strike, for example. This type of propane delivering tubing requires a type of "bonding", pursuant to the manufacturer's requirement. For more information regarding the safety of this product, recommendations for homeowners with this corrugated stainless steel tubing in their homes, we recommend that you visit the internet's http://www.pddocs.com/csst/default.aspx We also recommend that you visit the manufacturer's web site for their perspective regarding this issue: http://www.omegaflex.com/trac/newsuploads/CounterStrike_Brochure_2008.pdf
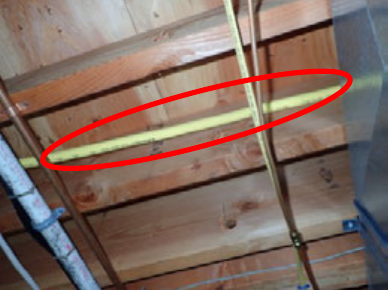
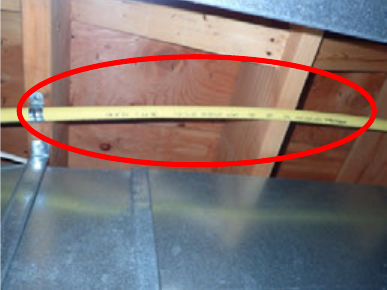
This house has been fitted with a radon mitigation system (see photo left of exterior components and see photo right of the manometer and piping inside the house). The system did not appear to be functioning as designed at the time of this inspection. We recommend you (or the seller?) contact the installing contractor to make the system functional. The installing contractor should also provide you with an orientation for the equipment and inform you of any maintenance that is required either by you or by them. Further, we recommend that obtain any warrantees or guarantees on this system from the installing contractor within 30 days of your closing.
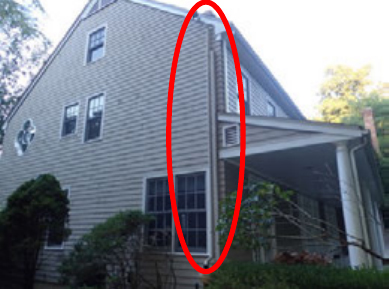
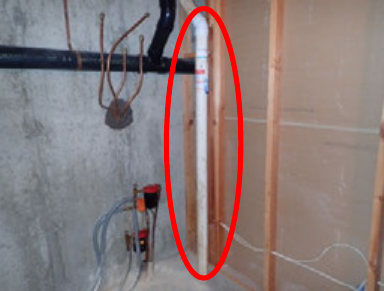
Installing a battery back-up power supply for the radon mitigation system, if the system is not being serviced by the installed generator system (see ELECTRICITY section of this report), will help ensure its uninterrupted operation in the event of a power outage. It is also recommended that the radon level in this house be tested periodically to insure the system's effectiveness.
Heating
Consistent with the information provided by the Standard Oil technician who evaluated the systems, the heating plants are oil-fired, steel, ThermoPride brand furnaces (serial #'s AJ6180060 and AJ618061/both model #'s OL16-125 - see photos above left and above right). The furnaces fired satisfactorily at the time of this inspection. They should be cleaned, including flue passages, and all components adjusted to operate at peak performance. The fan units and blades should be vacuumed and lubricated, as required, and the belts adjusted or replaced. All safety devices should be checked. The heat exchangers should be inspected for cracks and/or leaks prior to your closing (the heat exchangers can only be totally inspected by dismantling the furnace). If it cannot be verified that these furnaces and their components have been serviced and cleaned within the past year, arrangements should be made for that servicing.
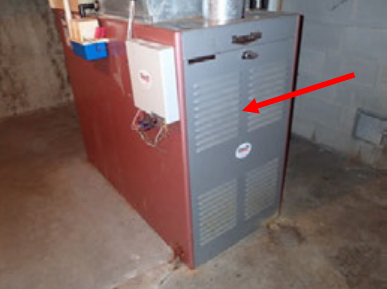
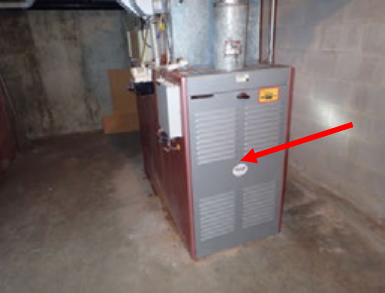
The furnaces appear to be approximately 23 years old. ThermoPride brand steel furnaces that have been properly maintained have an average useful life expectancy of approximately 25-30 years. Your plans should include budgeting to replace the furnaces when/before they fails.
The draft control installed on the smoke pipe of the heating plant in the left side unfinished basement area requires repairs to function as designed. This device controls the draft at the combustion chamber. A proper operating draft control will result in fuel economy therefore a draft control should be installed.
The smoke pipe-to-flue connection of the left-most unfinished basement area furnace is not completely sealed (see photo right). We recommend that this area be sealed and secured to help ensure that no off-gases escape into the basement space and living area.
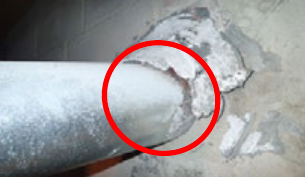
The humidifiers installed on both furnaces (see photos left and right) should be serviced in accordance with the manufacturer's recommended procedures. The humidifiers' bypasses should be open during the heating season and closed during the cooling season.
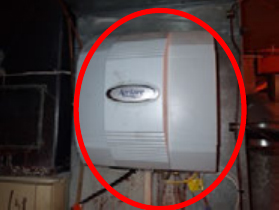
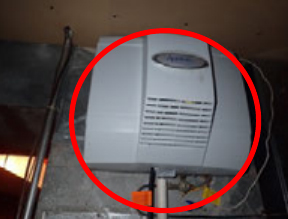
Humidifiers are prone to leaking (there was evidence of past leaking under these two humidifiers on the ductwork and on the furnaces’ jackets that appeared to be from previously installed malfunctioning humidifiers). If leaking recurs, the humidifiers should be serviced promptly to prevent damage to the heat exchangers and/or to the ductwork. We do not recommend the use of this type of humidifiers.
For best results, forced air system filters should be changed according to the manufacturers' guidelines, which is typically every 3 months. Filters should be changed more frequently, however, if dust levels are particularly high, such as during a remodeling or a construction project. Any system with a dirty filter can experience "pressure drop", which will lead to reduced air flow and it will put a strain on the system's components, which will lead to premature failure of the systems and/or their components.
The visible areas of the two, 14-year old 275-gallon, oil storage tanks were in generally acceptable condition (see photo right - red arrows). Oil storage tanks have an average useful life expectancy of 30-40 years but the life expectancy can be affected significantly by the environment around the tanks.
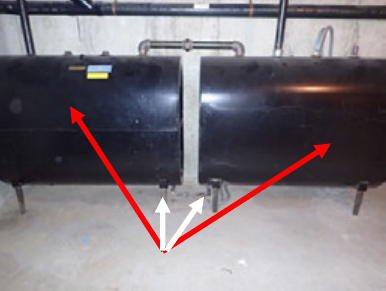
The main fuel (#2 heating oil) shut off valves are located in the basement at the bases of the aforementioned two, 275 -gallon oil storage tanks (see photo right - white arrows).
The oil supply pipes supplying the two furnaces (and the water heater) are covered with concrete and they run under the concrete slab floor (see photos left and right for example areas), preventing evaluation of the oil supply pipes. If the oil lines are not protected with plastic sheathing, the copper pipes are likely to be adversely affected by their contact with the concrete. It should be noted that oil could leak from these pipes below the concrete. We recommend that you have your oil supplier re-route the oil lines as required to remedy this condition and that the pipes be encased in protective sleeves to help prevent damage to the pipes.
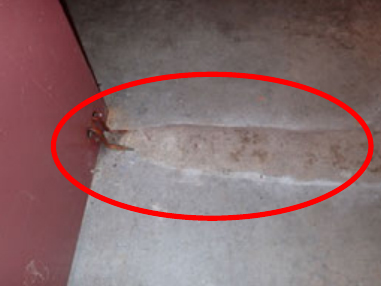
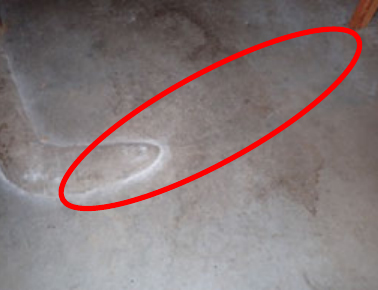
This house appears to have an abandoned or removed buried oil tank(s) (see photo left of clipped oil supply pipes penetrating the foundation wall). Abandoning or removing oil tanks should be done in accordance with all local, state and E. P. A. regulations. We recommend that you obtain the appropriate documentation confirming that the tank(s) has been abandoned or removed according to these regulations.
An active leak was observed at the fuel pump. The source of the leak and the cause should be determined and repaired as required to help prevent continued leaking and oil odors.
The heat distribution is multiple zones of forced hot air. All heat sources were warm, but some sources were warmer than others. There could be several causes for this condition, including the system needing to be balanced. A qualified HVAC service company should make the necessary repairs or adjustments for your comfort
We recommend that all heating supply ducts be insulated for better fuel efficiency.
All forced air systems, including ducts should be cleaned as required to help prevent possible accumulations of dust, dirt, allergenic substances, pathogenic substances and/or toxicogenic substances. We do not test for indoor "air pollution", which the Consumer Product Safety Commission rates fifth among potential contaminants. Nevertheless, inasmuch as health is a personal responsibility, we recommend that you have the indoor air quality tested as a prudent investment in environmental hygiene, and particularly if you or any member of your family suffers from allergies or asthma. We also recommend that all forced air supply and return ducts be properly sealed, as required for better energy efficiency and cost savings, to help the system function at peak performance levels, for better air distribution to each room of the house, to help extend the life of the system, for your safety and for various health and environmental reasons.
The finished basement is heated via one small independent electric resistant wall heater (see photo right). The heater was operated at the time of inspection and found to operate as designed. Be sure not to allow any electric cords, furnishings, draperies or flammable objects to rest against the electric wall heater while in use.
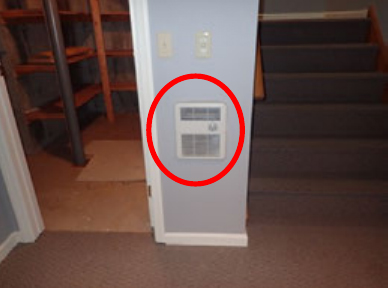
Heating Water
The water is heated by an independent, 70-gallon, oilfired, Bock brand, water heater (serial # 03083180T/ model # 71E - see photo left) with a recovery rate of approximately 185 gallons per hour. The hot water supply system was evaluated and found to provide adequate amounts of hot water to all fixtures tested, at the time of this inspection.
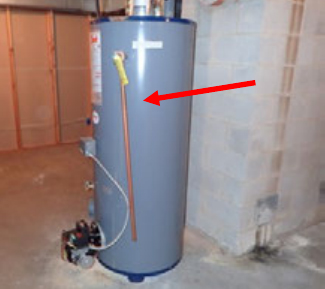
Oil-fired water heaters require annual inspection and servicing. At that time, all safety devices should be serviced and adjusted to operate at peak performance. All flue passages should be cleaned. It is recommended that water heaters be flushed periodically to help prevent internal rusting and to maintain an efficiency level.
A re-circulation system has been installed on the hot water supply pipes to help allow "hot water on demand" (almost instantaneous hot water at all taps in the house). You might consider consulting with a qualified, licensed plumber to install a timer mechanism for the recirculation system for better energy efficiency and savings.
Corroded fittings were observed at the top of the water heater. When the water heater is serviced, make any necessary repairs to help prevent leaking and consequential damage.
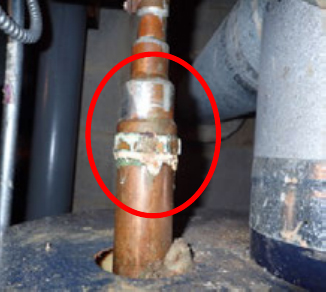
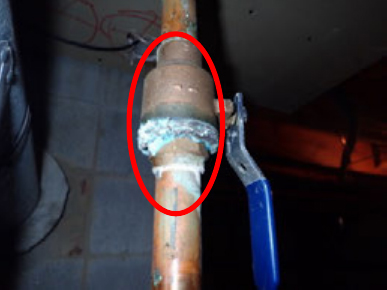
The smoke pipe-to-flue connection is not completely sealed (see photo right). We recommend that this area be sealed and secured to help ensure that no off-gases escape into the basement space and living area.
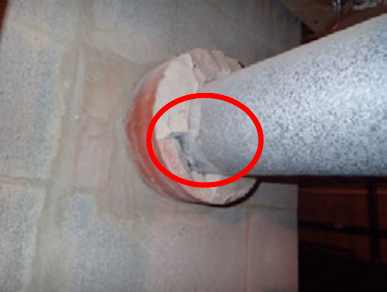
According to our inspector's thermometer, the undiluted hot water temperature was approximately 127.8 degrees Fahrenheit. It is recommended that the undiluted hot water temperature remain between 120 degrees Fahrenheit and 125 degrees Fahrenheit to prevent scalding and for your comfort. Make the appropriate adjustments for safety purposes.
The water heater appears to be approximately 13 years old. Water heaters that service well water supplies and that are properly maintained have an average useful life expectancy of 5-15 years depending upon the properties of the water they service. These units deteriorate from the inside out. We have no way of determining the interior condition of the water heater. Your plans should include budgeting to replace the water heater before/when it fails.
We recommend installing a pan and a drain under the water heater to prevent damage caused by a system failure or the discharge from the temperature/pressure relief safety device.
Most water heaters are equipped with an anode rod or with anode rods that serve as a "sacrificial" material to help prevent the interior tank from corroding. Replacement of depleted rods can extend the life of your water heater, so periodic inspections are recommended. Most water heater manufacturers recommend that the inspections are conducted by a qualified technician and at a minimum should be checked annually after the warrantee period expires.
Cooling
The Trane brand, electric, central air conditioning system's condenser/compressor (serial # R123XHL1F – see photo left) was activated using normal controls and it was found to be in acceptable working condition, at the time of this inspection.